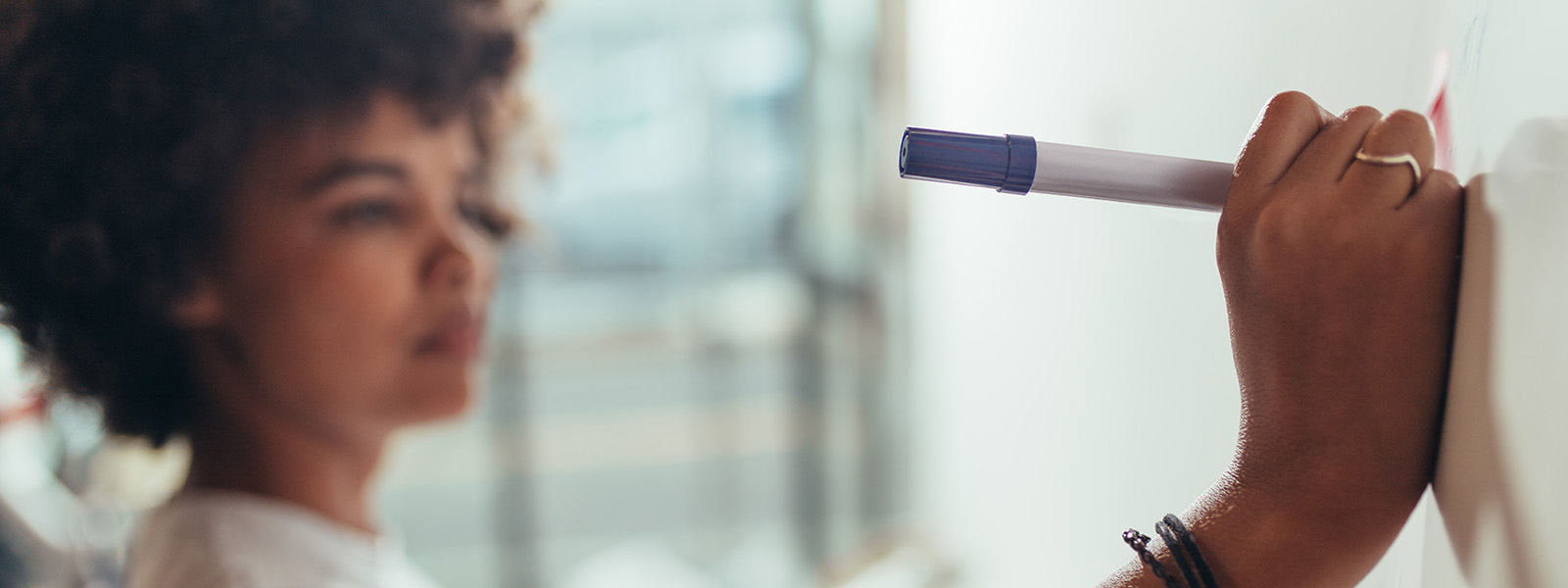
Despite juggling competing priorities, building resilient systems and processes within their organizations continues to be top of mind for business leaders today and is anticipated to be so for the foreseeable future. As such, the first logical step is to turn to existing methods and approaches that have been proven to be effective—of these, lean is a strong contender.
Starting from the beginning: the definition of lean
Defined as “a way of providing maximum customer value while minimizing effort, equipment, time, and waste in the production system,” lean is based on five principles:
• Value is defined according to the customer’s perception of it.
• Organizations must map the entire value stream and eliminate anything that doesn’t contribute to customer value.
• Products and services must flow smoothly to the customer with no interruptions.
• Customer requirements pull value upstream along the process.
• Perfection with no waste is the goal of the production system.
From an applicability perspective, the business process most commonly linked to lean is that of waste reduction, which is summarized into eight key types. This includes everything from motion to overproduction to underutilized talent.
Champions of lean methods: healthcare, services, and government
Since its inception, the application of lean has moved beyond manufacturing. In fact, there are some key industries where it has had a great impact.
Developed to optimize costs and drive innovation, lean healthcare-focused practices have been applied to various areas under the healthcare umbrella including patient care, training, and policy. In the services sector (e.g., retail, call centers), the importance of customer service drives the focus on continuous improvement.
Lastly, in the governmental sector, lean methods have led to the streamlining of bureaucratic processes, which have then provided workers additional bandwidth to focus on value-added services as well as the ability to pivot. Within each of these sectors, there are key types of waste that need to be reduced to meet their respective lean objectives.
Identify where lean can be leveraged during the Covid-19 era
Industry aside, there are many “quickly adoptable” and actionable recommendations based on lean practices that you can drive within your organization, including the following:
• Introduce virtual kaizen sessions: By scheduling regular kaizen sessions, your team will be able to collectively identify which processes and practice areas require improvement.
• Leverage online collaboration tools: By introducing online collaboration tools and modifying online workflows, you should be able to improve communications within your teams as well as with your customers.
• Work toward creating lean supply chains: By reducing unnecessary traveling and shortening lead times, you will drive agility within your supply chain structures.
How lean can help your organization with business continuity
By accessing our Insight Report, “Lean in a Covid-19 World: How Process Efficiency and Continuous Improvement Can Protect Your Business,” you will learn:
• The eight types of waste that should be reduced to drive operational effectiveness (e.g., transportation, inventory management, defects)
• The types of waste that need to be reduced to meet lean objectives in healthcare, services, and government
• The eight ways best practices in lean can be applied to your organization (e.g., facilitating gemba sessions to drive continuous improvement, identifying areas to improve crisis management, finding opportunities to drive innovation)
Add new comment