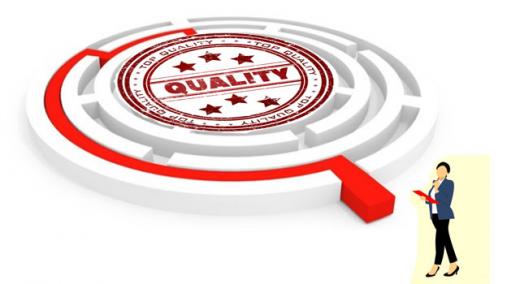
According to the Deloitte Automotive Quality 2020 report, auto manufacturers spend an average of 116 days annually on quality management system (QMS) compliance.
ADVERTISEMENT |
Layered process audits (LPAs), which can number more than a thousand audits per year, can take up many of those hours for companies that perform these short, frequent checks.
Executed correctly, LPAs can help sharply reduce defects and quality costs relatively quickly, but these high-frequency audits can also bury companies in administrative work if they’re not prepared.
This article examines classic problems standing in the way of quality, and how to fix them to make bigger and faster improvements.
Scheduling inefficiencies
Making and sticking to a schedule is fundamental to LPAs success, but the reality of scheduling daily, shift-level audits of critical to quality processes can quickly become overwhelming. Scheduling around paid time off and planned downtime is more complex and time-consuming, as is notifying auditors of their responsibilities.
…
Add new comment