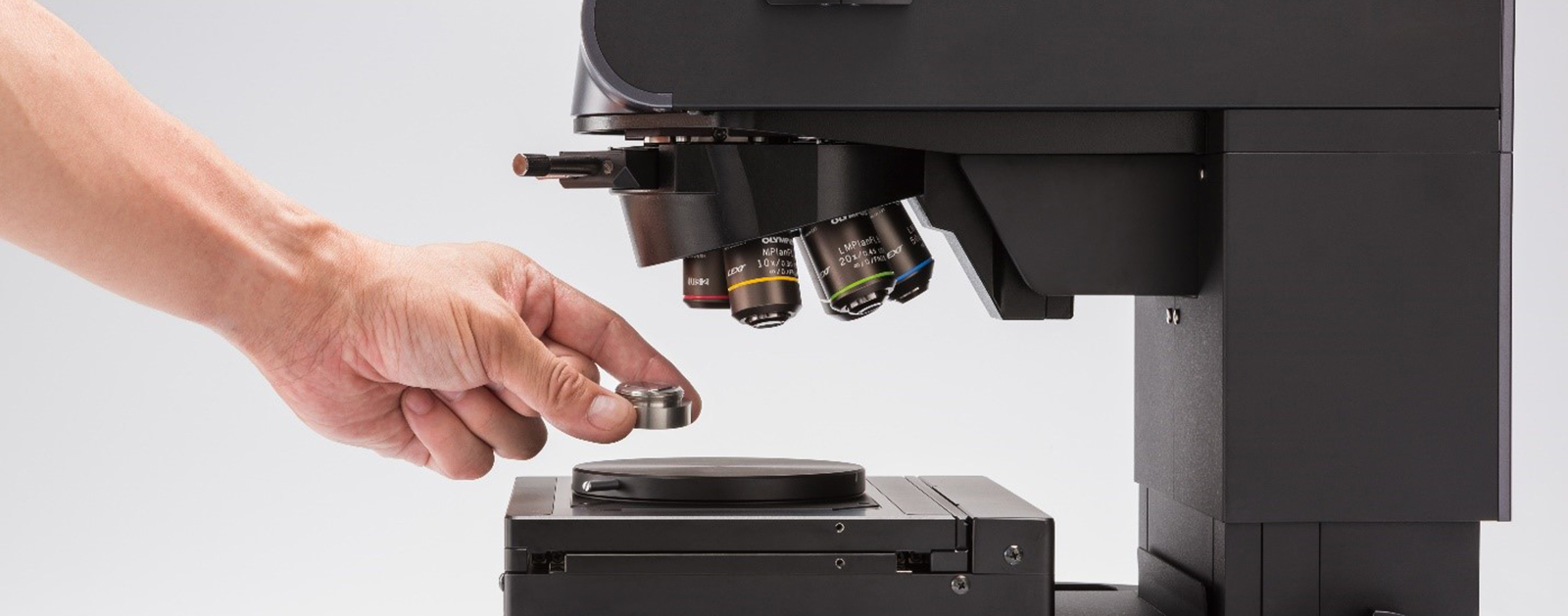
Modern 3D laser confocal scanning microscopes can resolve fine surface-topography detail as minute as a few nanometers, quickly and easily. It is the solution that advanced manufacturing industries turn to for efficient quality assurance surface inspections.
The changing needs of surface and interface engineering
Many of the modern conveniences that we have today are due to industrial engineering innovation and improvements. Much of this evolution and innovation depends on the precise engineering of surfaces and interfaces. For example, car engine performance and fuel economy depend on the surface finish of the piston and engine block. The nanostructured surfaces of anodes and cathodes of batteries ensure their reliable charging performance and long use life. The surface finish of electrical steel affects the energy conversion efficiency of the motors of electric vehicles, as well as the audio quality of amplifiers.
Surface and interface engineering is a critical aspect of various emerging technologies, and a lot of research and development efforts are focused on finding the best surface designs for next-generation industrial applications.
Ensuring the quality of the surface finish of parts in a manufacturing environment is challenging. Surface inspection has become a topic of discussion in many quality assurance departments across industrial disciplines. Quality assurance experts must achieve detail at the nanometer level while weaving through related practical constraints, such as maintaining the original surface condition, accelerating the inspection speed to meet the manufacturing throughput, and meeting the size and weight requirements of the final parts. They also need to think ahead to the future because the inspection process may need to be adapted if the manufacturing process changes. Conventional mechanical stylus profilometers cannot meet all these needs.
Advantages of laser confocal scanning microscopy
Because of their noncontact approach, optical profilometers are becoming the common choice for surface-finish inspection. Among the optical surface profiling tools used, laser confocal scanning microscopy is an ideal choice, especially when the surface topology is rough and complicated. The following list describes some of the advantages provided by the LEXT OLS5000 laser confocal scanning microscope from Olympus.
The LEXT OLS5000 3D laser confocal scanning microscope at a glance |
Precision imaging down to the nanometer level, reliably and easily
Olympus’ dedicated LEXT objectives enable the OLS5000 laser confocal scanning microscope to obtain sharp images and reliably acquire surface detail at the single nanometer level. These LEXT objectives are specially designed for surface metrology applications, and their 3D measurement performance is guaranteed.
The OLS5000 microscope’s 405 nm single wavelength laser beam provides high-resolution imaging and surface metrology measurements in minute detail. This noncontact optical approach not only makes taking measurements easy but also maintains the original surface conditions of the part.
|
|
|
The OLS5000 microscope has a small, compact footprint, enabling it to conveniently fit on most desktop workspaces. It is also easy to customize and modify the mechanical mounting scheme to adapt to new inspection requirements. Compared to SEM and AFM systems, the OLS5000 microscope requires minimal maintenance, making it a cost-effective inspection solution.
|
For additional information on the LEXT OLS5000 laser confocal scanning microscope, please visit the Olympus website.
Add new comment