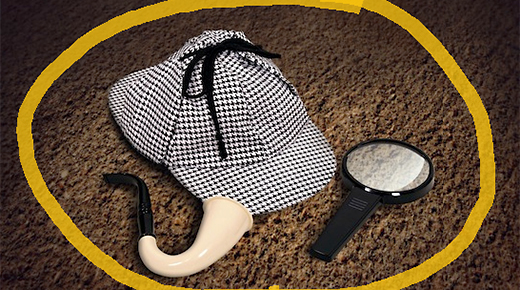
When an organization finds and eliminates waste, it gains a competitive advantage
During the mid-1940s, Taiichi Ohno established the Toyota Production System, which is primarily based on eliminating nonvalue-added waste. He discovered that by reducing waste and inventory levels, problems get exposed and that forces employees to address these problems. To engage the workers and therefore improve processes, Ohno developed many exercises.
One of his most popular exercises, the Ohno Circle, helps managers and students see process waste. During this exercise Ohno would take the manager or student to the shop floor, draw a chalk circle on the floor, then have that person stand inside the circle and observe an operation. His direction was simple: “Watch.”
Several hours later, Ohno would return, asking: “What do you see?” If the person saw the same problem Ohno had seen, then the exercise was over. If not, Ohno would say: “Watch some more.”
…
Add new comment