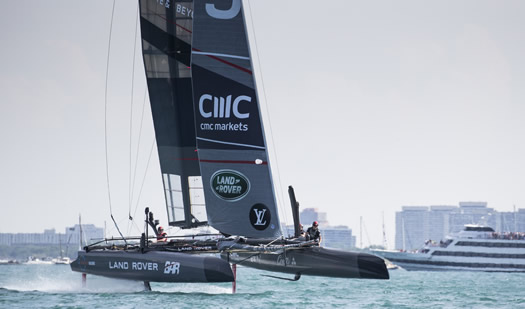
Land Rover Ben Ainsile Racing (BAR) is no stranger to cutting-edge technologies. The British yacht racing team, formed by four-time Olympic gold medalist and America’s Cup winner Sir Ben Ainsile, uses artificial intelligence, big data analytics, and most recently, additive manufacturing (3D printing) to gain competitive advantages. These technologies have been incorporated into daily use at Land Rover BAR by the team’s technical innovation group (TIG).
ADVERTISEMENT |
Renishaw, a global metrology company that also manufactures metal additive manufacturing machines, is a TIG partner. The partnership has allowed the team’s engineers to design and test precision custom parts quickly and cost effectively in the shop, and give it an edge on the water.
“We use 3D printing at three different levels within the team,” says TIG project manager, George Sykes of PA Consulting. “The simplest level is as a prototyping and visualization tool. We manufacture a large number of custom parts, and 3D printing allows us to make full-size prototypes in-house before we commit to a design.”
…
Add new comment