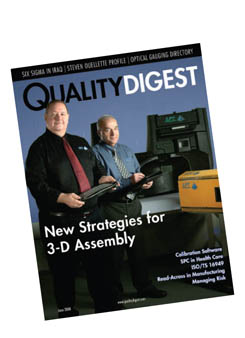
Rooting for Analysis
Would somebody please ask Mike Micklewright to stop making sense (“Why Root Cause Analysis Sucks in the United States,” http://qualitydigest.com/IQedit/
QDarticle_text.lasso?articleid=12753 )? He’s at risk of exposing a vast cottage industry of what Deming called “hacks,” and that could have incredible repercussions thereunto.
Just kidding about the hacks, of course. The real hacks, as Micklewright points out, are leaders who prefer tried-and-false methods of problem-solving. I liken it to how Congress blathers on about an issue and then passes legislation that has zero effect whatsoever, such as the “Airline Passenger Harassment Act of 2001.”
-- Jonathon Andell
I might not have chosen that title, but the article itself sums up the misconception or the inadequacy of how companies practice root cause analysis.
…
Comments
Add new comment