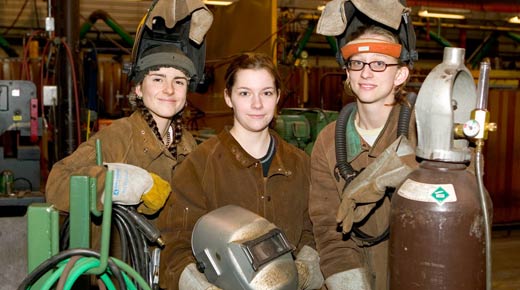
Vocational training though apprenticeships, allows young adults to learn and earn on the way to becoming a professional in a trade, art, or business.
Credit: Vancouver Island University
The U.S. manufacturing industry—once one of the most robust and powerful economic engines in the world—is now in a state of atrophy. Baby boomers are retiring in record numbers, taking their unique knowledge and skills with them as they head out the door for the final time. The people taking their place in the workforce—millennials and Generation Z—don’t have the training necessary to fill the void on the shop floor. As a result, owners are faced with the painful choice of asking competitors for help or shutting their shops for good.
ADVERTISEMENT |
I speak with our THOMASNET.com clients every day and, unfortunately, this is the reality facing many shops across the country. But it doesn’t have to stay this way. By analyzing how we got here, it’s possible to develop a plan to turn the tables on the skills gap and build a prosperous path for U.S. manufacturing going forward.
…
Add new comment