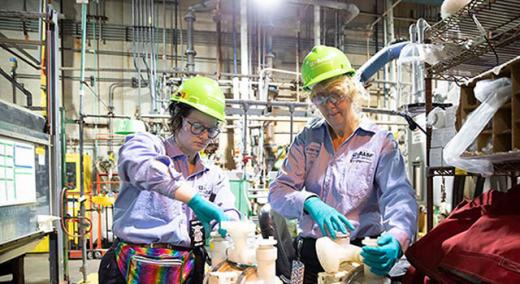
Many industries are embracing apprentice and trade programs in efforts to create a strong and reliable workforce for the future—and the manufacturing field is no exception. The BASF apprenticeship program began as a way for young professionals to find success through practical on-the-job training. Internationally, BASF offers apprenticeship in Germany and Switzerland as well as the United States.
ADVERTISEMENT |
In an interview with Quality Digest, Susan Emmerich, Ph.D., spoke on BASF’s North American Apprenticeship Development Program. As the program’s project implementation manager, she was able to outline key factors that make it a success.
QD: What progress have you seen so far with the program applicants, and what feedback have you received?
SE: We have had 90 percent of the apprentices successfully complete and place-off in full-time technician roles. According to our apprentice exit surveys, 92 percent of the apprentices said they would stay at BASF if offered a similar role elsewhere, and 92 percent said they see themselves in some role at BASF beyond three years.
…
Add new comment