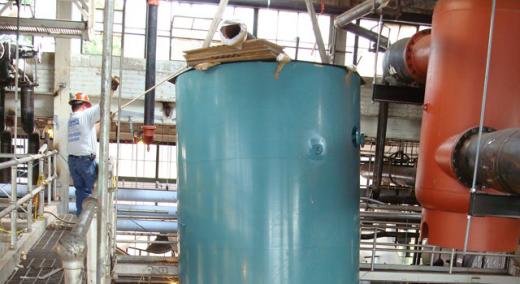
The pressure for industry to reduce harmful emissions and greenhouse gas emissions in particular has increased significantly in the past few years. Recently, President Joe Biden set an aggressive new target for the United States to reduce net greenhouse gas emissions by 50 to 52 percent from 2005 levels by 2030. The announcement, made at the Leaders Summit on Climate held in April 2021, challenges global leaders to raise their ambitions to tackle climate change on the scale required.
ADVERTISEMENT |
In December 2020, the European Union agreed to cut greenhouse gas carbon emissions by 55 percent by 2030 compared to 1990 levels. According to a recent report that has tracked the EU’s power sector since 2015, renewables surpassed fossil fuels last year (38% to 37%), indicating that industry is already pivoting away from carbon emissions.
…
Add new comment