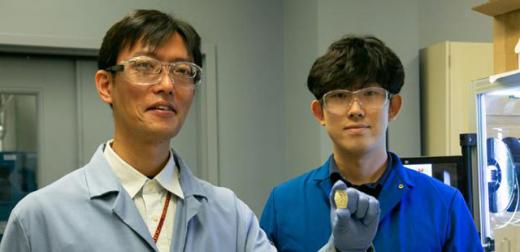
Researchers at the U.S. Dept. of Energy’s Oak Ridge National Laboratory (ONRL) have developed an upcycling approach that adds value to discarded plastics for reuse in additive manufacturing, or 3D printing. The readily adoptable, scalable method introduces a closed-loop strategy that could globally reduce plastic waste and cut carbon emissions tied to plastic production.
ADVERTISEMENT |
Results published in Science Advances detail the simple process for upcycling a commodity plastic into a more robust material compatible with industry 3D-printing methods.
The team upgraded acrylonitrile butadiene styrene, or ABS, a popular thermoplastic found in everyday objects ranging from auto parts to tennis balls to LEGO blocks. ABS is a popular feedstock for fused filament fabrication, or FFF, one of the most widely used 3D printing methods. The upcycled version boasts enhanced strength, toughness, and chemical resistance, which makes it attractive for FFF to meet new and higher-performance applications not achievable with standard ABS.
…
Add new comment