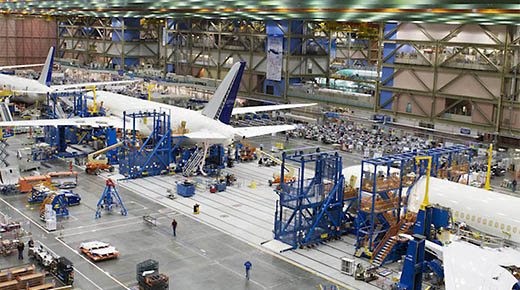
Body
In today’s economy, almost all manufacturing organizations are part of a supply chain, either as a buyer or a supplier themselves. Quite often they are both.
ADVERTISEMENT |
Outsourcing in traditional as well as new industries is growing rapidly. Consider that Boeing’s outsourcing evaluation grew from 400,000 parts with the 737 airliner series to 6,000,000 parts with the new 747-800 and it is easy to understand supply chain challenges as well as opportunities.
…
Want to continue?
Log in or create a FREE account.
By logging in you agree to receive communication from Quality Digest.
Privacy Policy.
Add new comment