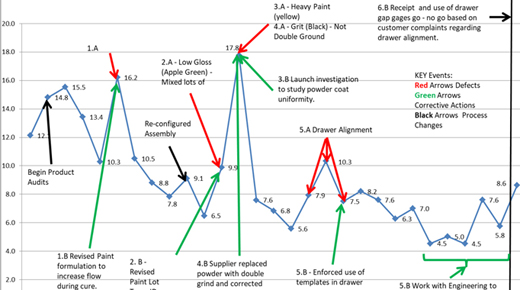
Metrics are an important part of an effective quality management system (QMS). They are necessary to understand, validate, and course-correct the QMS. They should be used to verify that it is achieving the goals and objectives defined by management. In an ISO 9001 system, metrics must be available to assess risk, and validate changes made to the QMS and individual processes. Metrics are also used to validate improvement and verification of corrective action implementation during the management review.
ADVERTISEMENT |
I have seen and used many metrics in the past, and in my experience not all metrics are equally good; in fact, many are totally inappropriate for the purpose for which they are being used. This article, the first in a three-part series, will help readers distinguish good metrics from bad—or as the title suggests, the downright ugly. Once the characteristics of a good metric are known, a bad metric can be converted into a good metric. This series is divided into three parts: Part one explains what a good metric is, part two identifies bad metrics and explains how to convert them, and part three looks at ugly metrics and explains why they have no hope for conversion.
…
Add new comment