Body
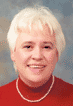
Considerations span the gamut of activities from multi-year projects to production-cycle times. They can range from the mundane (“Are the timers on the ovens accurate?”) to the critical (“How fast can we deliver blood to a hospital during a crisis?”)
…
Want to continue?
Log in or create a FREE account.
By logging in you agree to receive communication from Quality Digest.
Privacy Policy.
Add new comment