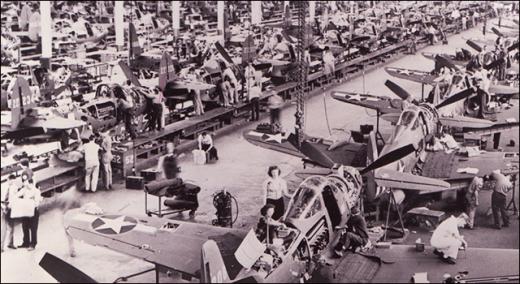
Managers the world over want to know if things are “in control.” This usually is taken to mean that the process is producing 100-percent conforming product, and to this end an emphasis is placed upon having a good capability or performance index. But a good index by itself does not tell the whole story. So, if you want to learn how to be sure that you are shipping 100-percent conforming product, read on.
ADVERTISEMENT |
Capability and performance indexes
There are four capability and performance indexes that are in common use today. While many other ratios have been proposed, these four indexes effectively summarize the relationship between a process and the product specifications.
The capability ratio uses the difference between the watershed specifications to define the space available and compares this with the generic space required by any process that is operated with minimum variance. This generic space required is computed as six times an appropriate within-subgroup measure of dispersion, Sigma(X).
…
Comments
Keys to QA - Dr. Wheeler
Excellent article as always from Dr Wheeler
It would be better if there was more focus on target performance, showing target lines on the histograms and control charts.
Hoe much can the indices differ?
Thank you Dr. Wheeler for this informative article!
Although I already read the chapter from your book, this was a welcome refreshment.
I have one question though:
Are there guidelines as to how much the indices can differ from another before a process is deemed unpredictable / off-centered based on the indices?
For exanple something like "if Pp > 1.25 Ppk then the process is off-centered".
This would be useful to give people some guidance who are not that familiar with the topic.
Add new comment