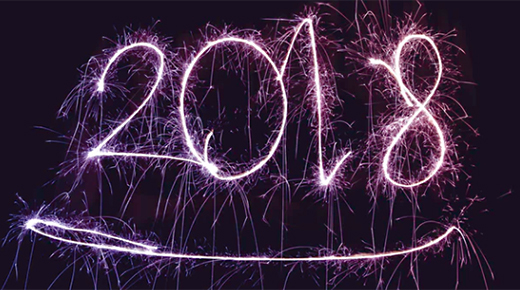
If you are a manufacturing company or a service provider, there is a good chance that you have heard about standards such as ISO 9001. In fact, you may already be certified. But whether you are certified or not, read on for some of the expected trends in the world of standards and certification for 2018.
ADVERTISEMENT |
ISO 9001 is here to stay
If you have ever been among the naysayers, such as “this is a waste of time” believers, or hard-headed “this does not apply to us” people, your time has come. If you think you are doing just fine without certification to ISO 9001, it is likely that you are losing money through inefficiencies. More to the point, you have probably already lost a contract or two to a competitor that was certified, whether you were aware of it or not. ISO 9001 is the bare-minimum standard that any good company should follow, and for this reason, all companies should adopt it. Although it has gone through various revisions during the past 30 years, ISO 9001 is undoubtedly a mature standard, and its auditors are experienced in certifying to it. So fight it no more; get your team together and invest in getting a good, basic quality management system into your organization.
…
Comments
Where is it stated in 2001:2015?
Where is the following requirement stated in ISO 9001:2015? Please state the clause number.
"Your employees must be trained and have a training plan."
Thank you, Dirk van Puten
Thank you for your
Thank you for your readership. Again, the intent of the article was not to interpret the standard outright, as much as it was to call out trends. While the standard may not require that, we see this expectation being called out by External Auditors. You can pick up a fight with them or use best practices or benchmarking. Having a training plan is a great practice but i'm sure there are others. Again, just be prepared that these trends of higher compliance expectation will continue. What was good enough 5 years ago is not good anymore. What was good 3 years ago may not be good enough anymore, specially for an organization who is looking for continual improvement.
No one has to be "qualified"
No one working in an ISO 9001 based quality manangement system has to be qualified. Employees have to be competent. The world "qualified" is purposely left out of the standard. Determine competence, ensure persons are competent, take action to acquire competence if needed, retain appropriate documentation. No required, documented training plan. No required "qualification."
This article is undoubtedly misleading if this article and 9001:2015 are not read critically.
Thank you, Dirk van Putten
qualified
@Dirk van Putten, Pl. Read 8.5.1 e of ISO9k15
Its adifferent matter when wetalk of auditor qualification.
Question Ms. Miriam is posing, "Is internal audit anyway less important than welding?"
The intent of the article was
The intent of the article was not to interpret the standard, but rather to point out the trends. The expectation from External Auditors is that your employees will be qualified somehow to be conducting internal audits of your company. Whether the standard calls it that way or not, the trend exist.
The difference is one of semantics
ISO 9001:2015 clause 7.2 requires that anyone whose work "affects the performance and effectiveness of the quality management system" (which would include internal auditors), be competent to perform their jobs. The difference between “competent” and “qualified” is one of semantics rather than practical significance. http://www.theauditoronline.com/competence-vs-qualification-personnel-certification-programs/ explains: “In ISO 19011:2011, Guidelines for auditing management systems, competence is defined as 'the ability to apply knowledge and skills to achieve intended results.' Competence-based certification means that the personnel certification body (PCB) is expected to examine a candidate’s knowledge, skills, personal attributes, and qualifications specific to the program and/or scope of certification. On the other hand, qualification-based certification relies on an applicant’s education and qualifications, rather than on the basis of measurable competence.” Note even that competence-based certification requires qualifications.
OSHA elaborates at https://www.osha.gov/pls/oshaweb/owadisp.show_document?p_table=INTERPRETATIONS&p_id=19389
29 CFR 1926.32(f) states: "Competent person" means one who is capable of identifying existing and predictable hazards in the surroundings or working conditions, which are unsanitary, hazardous, or dang- erous to employees, and who has authorization to take prompt corrective measures to eliminate them.
29 CFR 1926.32(l) states: "Qualified" means one who, by possession of a recognized degree, certificate, or professional standing, or who by extensive knowledge, training and experience, has successfully demonstrated his ability to solve or resolve problems relating to the subject matter, the work, or the project.
An RABQSA or ASQ certification in quality auditing is a “qualification” that indicates that the auditor is competent. While it's true that internal auditors do not have to be RABSQA or ASQ certified, there does have to be some kind of training record—again, a “qualification”—that is objective evidence that the person is competent to perform internal audits.
Fortunately, US laws (the
Fortunately, US laws (the CFRs) don't apply because ISO 9001 was made for international consumption, not US consumption. Quoting US laws to support a predetermined view doesn't work. It also smacks of more strongarming: "if you don't qualify your internal auditors, you're breaking the law!"
Which is, of course, nonsense.
The only requirements one is obligated to follow under ISO 9001 are those published in ISO 9001. Competence is determined by the organization itself (per 7.2.) and not by someone selling training classes on this website.
And there's nothing whatsoever about RABQSA or ASQ certifications that prove an auditor is "competent." It proves they paid for a short course. That's it. CB auditors who are generally expected to have RABQSA or IRCA qualifications show their incompetence every day, despite their pieces of paper. Again, this is fearmongering for the purpose of tricking people into buying something, because selling the training on its merits alone apparently doesn't work. If you have to resort to deception and fear, then the product you're selling is probably not worth it.
More from the usual suspects
As indicated by the other comments, the author just outright misrepresents the ISO 9001 standard to sell her services. It's shameful, but what's worse is that QD will apparently publish anything now, just to fill the space. Except for critical analysis of actual issues facing certification.
When can we get some honest articles about Takata, Kobe Steel, Amtrak, Deepwater Horizon, VW emissions or the dozens of other problems facing the ISO scheme? Doesn't the quality profession deserve at least a little integrity, rather than publishing commercial ads disguised -- poorly at that -- as an "article"?
Add new comment