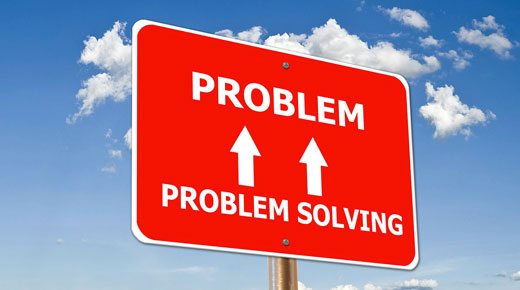
Whenever the term “nonconformance report” (NCR) comes into project home offices or construction and fabrication sites, it is often seen as a negative, and personnel are typically reluctant to accept it as a positive and powerful tool to improve. Perhaps, the “non” in nonconformance is the reason for this. This article explains why NCRs should be seen as friends rather than a foes, and how they can be used to improve a company’s projects, products, and services as well as its overall performance.
ADVERTISEMENT |
First of all, why are NCRs your friends? Here's a short list:
…
Add new comment