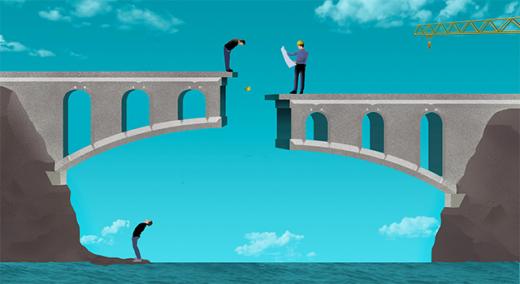
A company’s quality management system should have a formal, effective, and efficient corrective action and preventive action (CAPA) program so management can stay informed and correct existing business problems. The data output and corrective actions from a CAPA program can help prevent recurring problems and prevent new ones, giving management key indicators of what is going wrong and where to change the organization.
ADVERTISEMENT |
Per ISO 9000:2015—“Quality management systems—Fundamentals and vocabulary,” the following definitions are provided for correction, corrective action, and preventive action:
• A correction is an action to eliminate a detected nonconformity (examples include rework, scrap, reprocess, reject, or upgrade).
• A corrective action is an action executed to eliminate the cause of a detected nonconformity and to prevent the recurrence.
• A preventive action is taken to prevent occurrence or prevent it from happening in the first place.
There’s a distinction between correction and corrective action, according to the ISO standards.
…
Add new comment