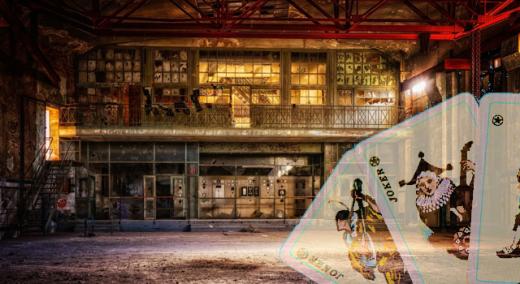
When it comes to ongoing certification of your quality management system (QMS), whether it’s certified to ISO 9001, ISO 13485, IATF 16949, or AS9100, how many times have you found yourself “preparing for an external audit?”
ADVERTISEMENT |
Picture the scene: You’ve got the dates set on the calendar months in advance for when the certifying body (CB) auditor will be onsite. For several weeks, you’ve been communicating in company memos and meetings about the upcoming visit. You’ve started to lay out Gannt charts and action-item lists for things that you need various departments and individuals to check up on and clean up as you inch closer to the arrival day. You’ve developed a carefully curated path to lead the auditor so that they see only the things that you want them to see. You’ve trained personnel in that area on the proper responses to auditor questions. You must make sure that everything appears to be in order when the auditor arrives.
Notice the statement, “Everything appears to be in order.”
…
Comments
Have you Truly Integrated QMS Requirements Into Your Business Pr
INCREDIBLY well said and so very true. Sadly, most managers either don't understand the concept or just refuse to commit to it. They would rather waste time and money talking in tired cliches and building smoke screens than practicing what they want to claim.
Too true
Perfect description which can be summed up as 'do as you say, say as you do". The trick? Well... there is no trick. Do what you say and actually say what you do.
Add new comment