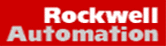
The study, based on interviews with 582 OEMs and end users, compared the two groups’ views on important relationships issues like design cycle responsibilities, buying behaviors and communication channels. It revealed that the groups have similar views in several areas. For example, 85.3 percent of end users and 86.3 percent of OEMs believe OEMs are a primary source of good industry trend advice.
The most divergent responses pertained to questions about procurement costs. Almost 95 percent of OEM respondents believe end users tend to choose machines and components based on lowest cost, while only 78 percent of end users agree with this statement.
The study suggests that OEMs and end users can improve their relationships by having better channels of communication, involving OEMs early in the design cycle and providing more customer support. The top comment—made by a third of OEMs and end users—suggested that having a better understanding of design specifications enhances the business relationship.
…
Add new comment