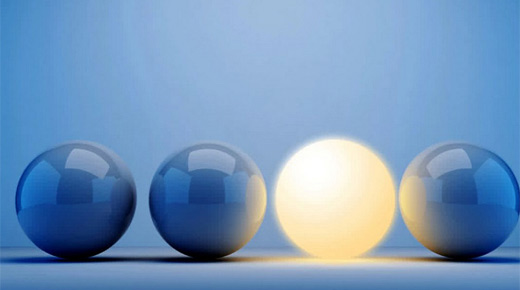
What's the big difference between visual and lean? Answering that question brings us closer to understanding our premise for the short series I began in issue 23 of The Visual Thinker (May 27, 2017), with the article, “Lean Alone Is Not Enough.” But first we must raise the question under the one I just asked: Why is an answer important?
The core difference between visual and lean is the medium each targets. Visual pursues embedded information and, therefore, adherence. Effectively implemented, the result of visual is stability—and stability creates reliability and repeatability (with a straight arrow pathway to sustainability). I rush to add that visuality produces stability even in low-volume/high-complexity production—in fact, especially there.
Lean targets pull along the critical path. Lean, therefore, targets time—and its corollary, speed. The combination of the visual and lean—embedded information and time—provides the enterprise with a powerful platform for growth. Because visual and lean are both waste-reduction strategies, in combination they become a powerhouse for any company's pursuit of operational excellence: the visual-lean alliance.
…
Comments
Lean is not TPS...
A point of clarification that some might find helpful is that in the Toyota Production System the visual workplace is a standard 'tool' or methdoology. It is not separate by any means. so it isn't an either/or proposition.
Can you elaborate on why you believe that pull is not appropriate for a depot but flow is? From my experience I primarily agree on that but I am curious as to your reasoning.
Depots, Service centers, medical labs, distribution warehouses, etc. are all very similar in that their 'orders' are 'somewhat' unpredictable (not as bad as some want to think) and the work to be done certainly fits the mixed model system as the work to be done is highly variable. However in my expereince with all of these systems I have been able to eliminate waste including queue time to accelerate the flow. Without having to negatively effect quality or reliablity. So time is certainly - at least in my experience - an element that can be improved by reducing it. And the visual workplace has been a critical element in achieving and sustaining these improvements.
Add new comment