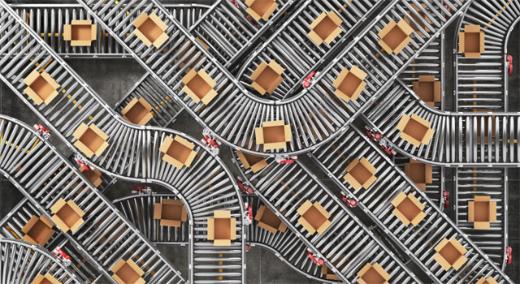
Motorized drive rollers (MDR) are an efficient and safe way to move large or heavy products down a conveyor line. They are also a key part of zero pressure accumulation, which allows conveyor systems to accumulate product without collision.
ADVERTISEMENT |
In traditional conveyor systems, products can back up behind an accumulation point and potentially exert hundreds of pounds of pressure on the product. Using MDR and individually monitored and managed accumulation zones eliminates collisions. Such zero pressure accumulation systems can easily handle large heavy products on a conveyor line.
…
Add new comment