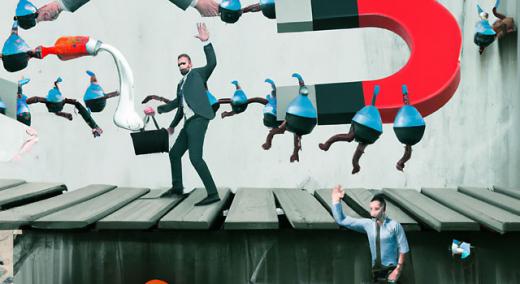
When Nico asked me if I wanted to collaborate on this year’s challenges blog, my second thought after agreeing to the idea was a scene from the 2007 film Music and Lyrics, which I likely haven’t seen since approximately 2008.
ADVERTISEMENT |
Why this popped into my head is unknown, but ha—pop! I had forgotten that Pop! was the name of Hugh Grant’s singing group and part of the title of their hit song. The hip move! I may have been over-caffeinated or under-caffeinated—the line can be so fine—but as Nico and I started talking about our findings and plotting our structure, that’s what came to mind. Music and lyrics! Peanut butter and jelly! Cinnamon and raisins! We’ve got this!
…
Add new comment