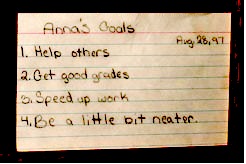
It recently dawned on me that Anna’s list cuts to the heart of what manufacturers strive for and what many quality gurus recommend. I’ll try to explain the connection.
Please consider the importance of having your goals or objectives clearly identified for all to see. (If you can’t explain where you want to go, how can anyone tell if you’re making progress?) In manufacturing, we also like our goals to be concrete and measurable, so we can quantify how much progress we’re making. We’d also like to widely distribute convenient status reports, sometimes known as metrics.
Let’s consider Anna’s goals:
Help others
…
Add new comment