Body
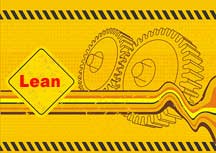
Literature review
Fred E. Meyers has described lean as “a concept whereby all production people work together to eliminate waste.” Peter Brunn and Robert Mefford introduced their research article "Lean Production and the Internet" by stating that many manufacturing firms around the world have adopted lean production as a strategy to increase their global competitiveness. Some firms have made much progress in implementing lean production in their factories.
…
Want to continue?
Log in or create a FREE account.
By logging in you agree to receive communication from Quality Digest.
Privacy Policy.
Add new comment