Body
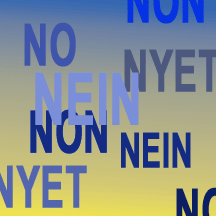
"Therefore is the name of it called Babel; because the Lord did there confound the languages of all the earth…"
—Genesis 11:9
The story of the Tower of Babel occupies but nine verses of the Book of Genesis, but it contains a valuable lesson for today: a multiplicity of languages makes it harder to run a workplace effectively. This is especially true when the quality system relies on controlled documents, as required by ISO 9001 and ISO/TS 16949. Robert M. Bakker cites in his "Why companies fail quality audits" (Manufacturing Engineering) three predominant sources of quality system nonconformances:
…
Want to continue?
Log in or create a FREE account.
By logging in you agree to receive communication from Quality Digest.
Privacy Policy.
Add new comment