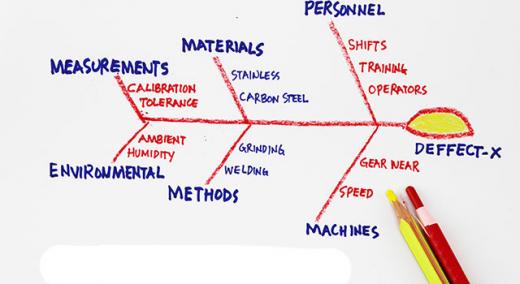
Root cause analysis is not a singular way to an answer. It is a conceptual framework for investigating the true reasons behind the events we observe. Many frameworks are available to execute RCA that have been tried and tested by experimenters. None of these methods are foolproof, but they provide a solid base for how to go about root problem investigation. Let's discuss some of the prominent tools and techniques.
ADVERTISEMENT |
Each of the RCA tools has its own merits, and certain methods are more suitable for different industries and the types of problems that are being investigated. Each company and its management team should have a protocol to adhere to when conducting RCA. Different companies might prefer different techniques. In some instances, external consultants might be brought in to conduct RCA. In such cases, the consultants will have a preferred technique or a combination of techniques they use to conduct RCA. This is one of the reasons why it is hard to create a universal template for RCA that everyone can follow.
Oftentimes, the company will have a preferred RCA technique. If that one does not give the needed answers, other techniques might be explored.
…
Comments
RCA - 5 Why's
I was taught that you have not reached the final why, in the 5 why's method, until the answer returns a process improvement. In the example you give, I would say the answer to the final why would be that the equipment needs to be inspected more often the verify that metal shavings are being properly cleaned out.
Add new comment