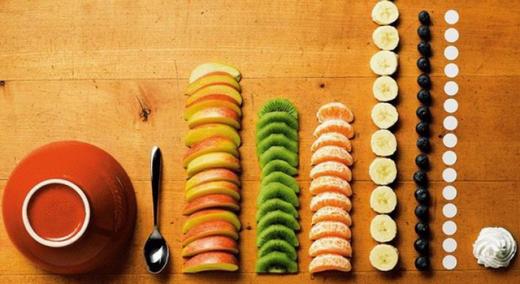
Sometimes I see people chasing their tails when trying to troubleshoot a process. This usually (though not always) follows a complaint or rejection of some kind.
A few years ago I posted “Organize, Standardize, Stabilize, Optimize” and talked in general terms about the sequence of thinking that gives reliable outcomes. This is a series of questions that, if asked and addressed in sequence, can help you troubleshoot a process. The idea is that you must have a very clear yes to every question before proceeding to the next.
ADVERTISEMENT |
Question 1: Is there a clear standard for the outcome?
Why is this important? Because if you don’t have a clear expectation of what “good” looks like, then your definition of “not good” is subjective and varies depending on who, what, and when things are being looked at.
…
Add new comment