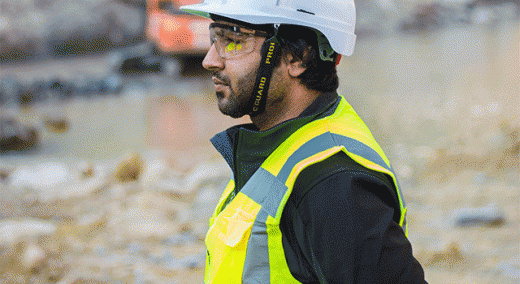
According to “The 2022 State of Employee Safety Report,” 79 percent of employees say they’re concerned about their health and safety at work. Workplace safety policies along with various technologies can be effective tools for preventing injuries and increasing employee productivity. Overlooking or underutilizing these resources can leave you vulnerable to serious problems and legal consequences.
ADVERTISEMENT |
Engaging the whole company, including upper management and every single employee, in using these resources is the only way to truly achieve facility safety. Here’s how.
What is facility safety?
Facility safety happens when an organization has the appropriate infrastructure in place to ensure the working environment is as safe as possible for all employees. It requires developing standard operating procedures (SOPs) and using best practices to address and resolve safety risks.
…
Add new comment