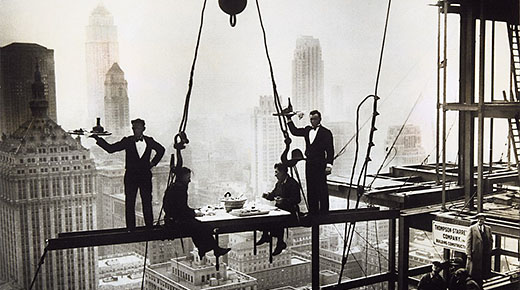
One thing you can say about that critical commodity called steel: It gets around. Ancient ironware excavated in what is now Turkey has been dated to 1800 B.C. Some 1,200 years later, blacksmiths in Sri Lanka employed furnaces driven by monsoon winds to produce a high-carbon steel. The Tamils of southern India enjoyed a lucrative steel trade with the likes of Alexander the Great.
ADVERTISEMENT |
Romans, Chinese, and Syrians all added improvements to this metal wonderworking that could turn chunky iron ore into swords and sewing needles. Europe came late to the game—circa 700s—but its steel mills were precursors to the first factories of the Industrial Revolution.
A modern representation of a medieval steel mill in Sweden
Then it was America’s turn.
…
Add new comment