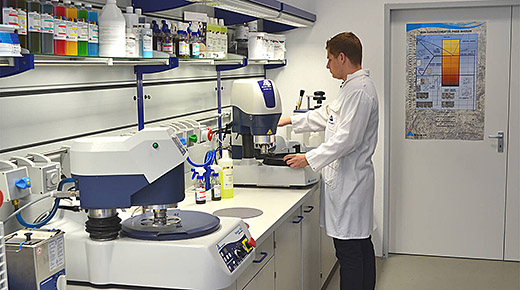
For manufacturers in diverse sectors such as automotive, aerospace, electronics, and medical device, there’s little question that ensuring great quality would be impossible without the proper testing of materials. And proper material testing applications begin with reliable and repeatable preparation methods.
ADVERTISEMENT |
Metallography is the microscopic study of the structure and components of pure metals and metallic alloys. For the purposes of test and measurement as well as quality control, understanding the microstructural flaws, tensile strength, hardness, and other attributes found in fasteners, coatings, and components is obviously of great import. Being able to accomplish such testing efficiently and accurately allows factories to achieve necessary throughput.
Material preparation
“There’s no better way of judging the structural and long-term properties of the material than looking at the structure of the material itself,” says Mike Keeble, Ph.D., U.S. lab and technology manager for Buehler, a leading manufacturer of scientific equipment and supplies for use in materials analysis.
…
Add new comment