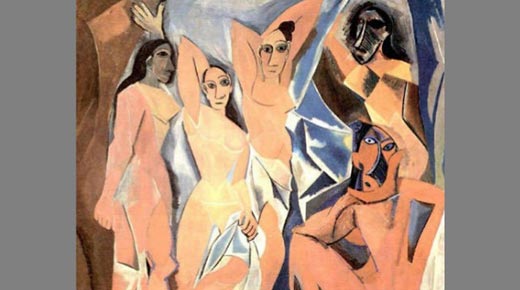
In lean we talk about “seeing the waste” and using visual tools. Many of us who use these terms have had a lot of training in engineering, manufacturing, and other highly technical areas. However, the skills needed to “see” problems may lie more firmly in the study of art.
ADVERTISEMENT |
I recently read an article about some forward thinking companies that are creating art programs to help them identify safety problems. Why would we want to do this? When we are trying to see waste opportunities or see safety opportunities we should be asking ourselves:
• What do I see?
• What does it mean to me, other workers, and productivity in the area?
• What should I do about it?
If we understand concepts in art education, we may be able to overcome some of the biases that we all have when we are observing what is taking place on the shop floor. The following are some of those biases:
…
Add new comment