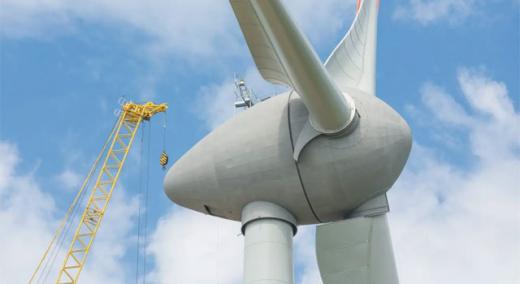
During a recent interview with Dirk Dusharme, host of Quality Digest’s QDL, we discussed project-based manufacturing, the umbrella term that covers the types of manufacturing done on a project-driven schedule. Some refer to this as “engineer to order” (ETO), a niche in engineering-focused manufacturing.
ADVERTISEMENT |
As repetitive high-volume manufacturing has been offshored to China, Vietnam, and other locations, many U.S. manufacturers have moved toward mass customization (sometimes called “made to order”) for the consumer market. These typically involve a base product to which the customer can add variations. Project-based products, on the other hand, are unique to each customer from the ground up and have grown significantly now that the technology is able to support it.
Project-based products are largely targeted at the B2B customer. The types of industries that are project-based include those that manufacture equipment for wind turbines, aerospace and defense, and biotech, as well as contract pharmaceutical developers. These projects tend to be long-term and complex.
…
Add new comment