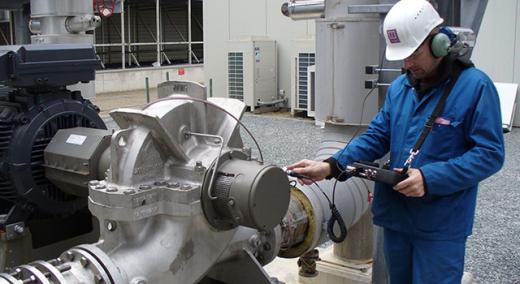
There are various nondestructive testing (NDT) methods we can employ to evaluate the condition of different machine components, without the need to stop and disassemble the equipment. Vibration analysis is a prominent NDT tool used across many industries.
ADVERTISEMENT |
In this article, we will take a good look at the intricacies of the vibration analysis process, parameters, tools, and use cases.
Why vibration?
Vibrations occur in all moving machinery while in operation. Every material has a characteristic pattern of vibration under specific conditions. Measuring, recording, and studying the changes in these vibration characteristics can help us understand the changes in the test material itself.
What is vibration analysis?
Vibration analysis is a process that uses vibration signals to identify anomalies in vibration patterns. A change in the vibration pattern indicates a change in the physical properties of the test object.
In equipment maintenance, vibration analysis helps us track and evaluate the condition of our equipment.
…
Add new comment