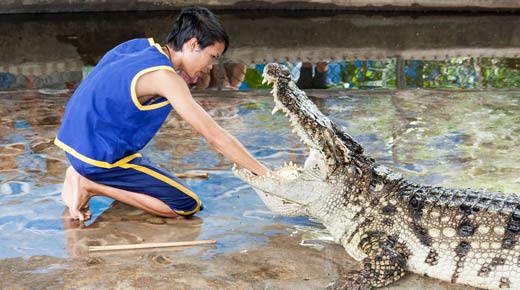
The dynamic of risk management and compliance seems to be experiencing a shift toward risk management in operations, and learning to pay attention to detail in order to leverage it.
ADVERTISEMENT |
The biggest question often asked is, “I’m aware my company needs to pay great attention to the detail of risk, but I don’t know where to start, or even how to put it into practice.”
This is a normal practicality with which most quality professionals struggle. As for what you can do about risk, it’s important to first focus on the process of collecting and analyzing your risks. There are many common, simple, and effective tools to help make risk management a practical option for your business.
After risk is mapped out it can be better controlled. Risk tools make it possible to delve a little deeper into the overall scope of risk management from a company and operational perspective using ISO standards.
…
Add new comment