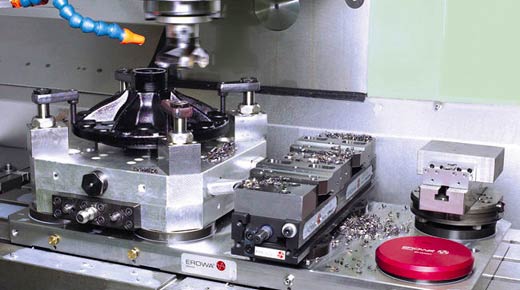
What do you think of when you think work holding? A vise, hydraulic clamps, vacuum plates, toe clamps, magnets, glue? Absolutely, but this is only half of the equation. What about the interface between these components and the machine tool? This is equally important, if not more so because it dictates the time it takes to change your work holding, which in turn has a significant effect on your spindle uptime.
ADVERTISEMENT |
By investing in a quick-change pallet system (aka zero-point clamping system), most companies report a return on their investment in only a few months. From then on, it is pure cost savings year after year.
When work holding must be changed on a typical t-slot table, a skilled operator must unfasten the work holding with the many screws holding it in place, clean the table, load the new work holding, and then indicate it by reestablishing the offsets. Not only are the people who are capable of doing this becoming a scarce resource, but it takes time, no matter how skilled your operator is. Depending on the complexity of the setup and the skill level of the operator, this could take anywhere from 45 minutes to 3 hours, during which time the spindle is idle.
…
Add new comment