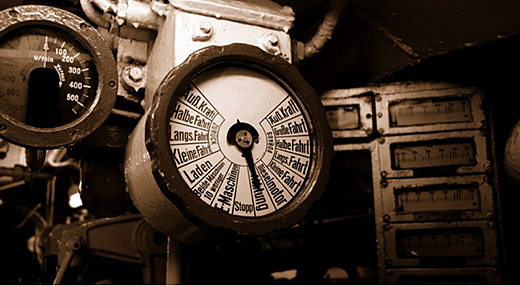
Measurement devices in manufacturing facilities are as ubiquitous as Skittles in trick-or-treat bags. Some companies have thousands of devices in their inventories and depend on them to provide accurate information. This is why timely calibration of all measurement devices is critical to manufacturing efforts.
ADVERTISEMENT |
While process improvement initiatives, including statistical process control (SPC), can get the greatest attention in manufacturing environments, frequently the backbone of a quality improvement effort is the quiet, often unnoticed, measurement devices that represent an organization’s commitment to consistency and accuracy. These silent workers give vital information by providing meaningful measurements and assurance about whether products are ready to ship or not. They deserve to be treated as a top priority.
Yet a critical, and often overlooked, part of the journey toward reducing variation and continuously improving is developing confidence in the system used to measure the process, parts, or products. Most of the improvement efforts in organizations are spent on reducing variation among products. Little, if any, attention is paid to the variation introduced into the overall picture due to the measurement system.
…
Add new comment