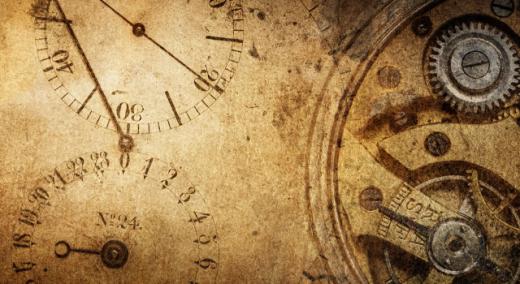
The RGM Watch Co. was founded by American watchmaker Roland G. Murphy. His career and interest in horology (the art or science of timekeeping devices) began as a teenager while working part-time for a clock company. Later, he enrolled in the Bowman Technical School of Watchmaking, and in 1986, Murphy was accepted into WOSTEP (Watchmakers of Switzerland Training and Educational Program).
ADVERTISEMENT |
After finishing WOSTEP, he worked in product development for the Hamilton Watch Co. until he founded the RGM Watch Co. in 1992.
|
RGM Watch sales are conducted on a personal, one-to-one basis. Customers who visit the company are often greeted by Murphy himself, who openly shares his passion for classic watch design, innovation, and craftsmanship as he discusses the custom design features that are often requested. RGM employs a team of 11 people and produces “a few hundred” watches a year, priced from $3,500 to $95,000, depending on design and material.
…
Add new comment