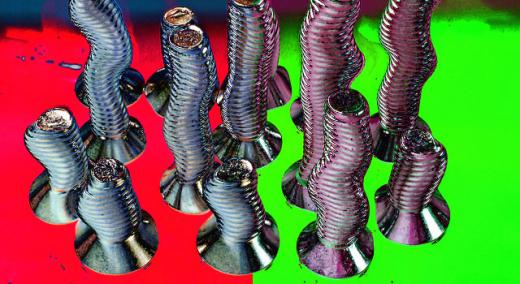
Adapted from "Squashed Bolts" Credit: Tudor Barker
‘I just want to avoid spinning gauges all day.”
We hear this from manufacturing professionals all over the world. We were discussing this recently with a manufacturer in Wisconsin that machines large quantities of threaded parts. Their customer requires them to “go” and “no-go”-verify every part. They were dealing with this requirement the way many plants do: Operators stood by and spun a gauge into every thread with their fingers. Unfortunately, this method was not only burdensome but also allowed plenty of room for operator error and repetitive-motion injury.
ADVERTISEMENT |
Our mission at New Vista is to work with manufacturers like these to provide the knowledge and tools they need to overcome thread quality obstacles, so they can stop spinning gauges with their fingers. This article, as part of that mission, presents an introduction to thread gauging.
…
Add new comment