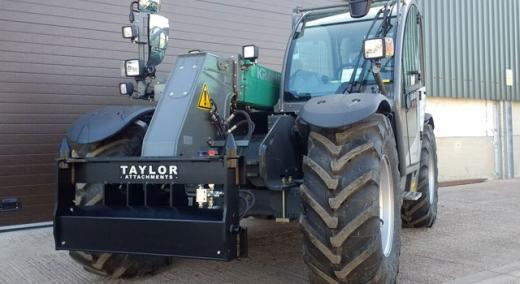
Taylor Attachments, based in the United Kingdom, custom designs and produces tractor headstock conversion brackets. These are attachments for farm handlers and loaders, for mounting everything from buckets to forks, grapples, saws, carriers, bale stabbers, grabbers, hitches, backhoes, tillers, yard scrapers, and more. Clients also send the company legacy equipment, which Taylor’s specialists precisely measure and reproduce using the latest materials and technology.
ADVERTISEMENT |
In the past at Taylor, this was a 100-percent manual process, which meant a busy 7 to 12 hours of making drawings using rulers and calipers, and pens and pencils to trace out parts and components on cardboard and paper, before creating mock-up prototypes for testing and secondary alterations.
…
Add new comment