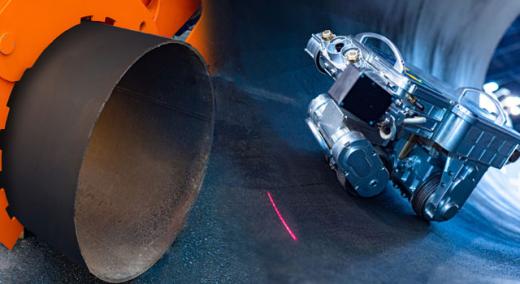
Although remote inspection has been a topic of discussion in the oil and gas industry in the past, it has recently been getting more attention during the Covid-19 pandemic. Many oil and gas operators, as well as engineering, procurement, and construction (EPC) contractors and suppliers have come forward to discuss this topic with an open mind and explore possibilities. Remote inspection is perhaps the need of the hour, but it can also be the future of inspection.
ADVERTISEMENT |
What is remote inspection?
Remote inspection is an alternative to an onsite physical inspection in which the person performs inspection activities remotely using sophisticated technological tools. It’s many benefits include:
• Elimination of personnel risk exposure to hazardous conditions and dangerous tasks in harsh environments
• Global collaboration and optimization of workforce use
• Inspection cost reduction
• Real-time feedback
• Flexibility
• Eco-friendly by helping to reduce overall global carbon footprint
Success factors for remote inspection
Vision
“It’s not enough to be busy, so are the ants. The question is, what are we busy about?
—Henry David Thoreau
…
Comments
The tools have been simplified
This is an intersting overview. Remote Inspection is not just utilized in the Oil and Gas industry as this article aludes. Construction Managers in all industries are using it, routinely these days. Infact, the Telecom industry has been using Remote Inspection for most of the 5G build out since 2017. Moreover, there is now dedicated Remote Inspection software tools available for companies. So you're not reliant on Zoom, or Teams. One example is CloudVisit's software, which simplifies generation of Inpection Test Plans throught the use of a flexible checklist format. It even consolidates collection of inspection evidence in the cloud. The platform is simple and intuitve which helps to minimizes training. Moreover, you can actually record the entire inspection and save it as evidence for governmental regulators, and to handover to customers for closeout packages. [Post was edited by Quality Digest]
Add new comment