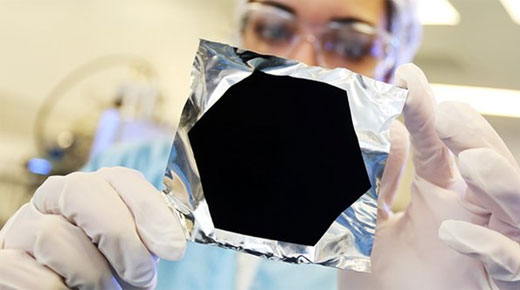
Color is our perception of reflected light across the visible spectrum. When light hits an object, it absorbs some rays and reflects others. The color of light that reflects back into our eyes is the color we perceive. The more light an object absorbs, the darker it appears.
ADVERTISEMENT |
With black, very little light is reflected. Pure black in the presence of light wasn’t achieved until 2014, when Surrey NanoSystems announced the invention of Vantablack. This high-tech artificial substance absorbs 99.965-percent of all light that hits it, from the ultraviolet, through the visible, and well into the infrared spectrum. When applied to an object, Vantablack makes the object look like a flat, bottomless void in space. Here you see a crumpled piece of aluminum foil, with Vantablack covering the middle. There is so little reflection, you can’t even perceive the wrinkled texture!
…
Add new comment