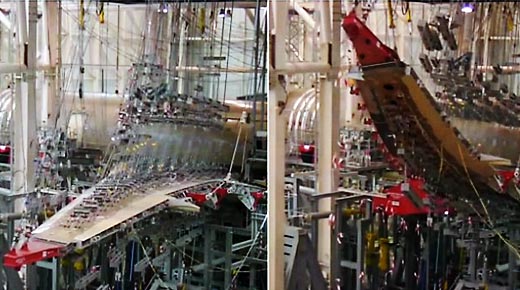
Scientists have found a way to improve the simulation of the onset of failure in airplane wings.
Credit: Airbus
How do jumbo-jet designers develop resilient materials for modern airframes, while still bringing in their projects on time and on budget? Before they prototype a new material, they depend heavily on computer simulations to indicate how it will perform—and scientists at the National Institute of Standards and Technology (NIST) are making those simulations more effective.
ADVERTISEMENT |
A team including NIST scientists has found a way to improve the process of simulating the onset of failure in the materials used to build airplane wings. Understanding this initiation point is critical for predicting when and how wings fail. Their method shows designers how to put a particular sample through a series of stress scenarios to efficiently determine the amount of stretching that will cause it to break.
The approach, according to NIST physicist Paul Patrone, could help address one of the key factors that reduces the effectiveness of simulations: uncertainty in their prediction of the wing’s strength.
…
Add new comment