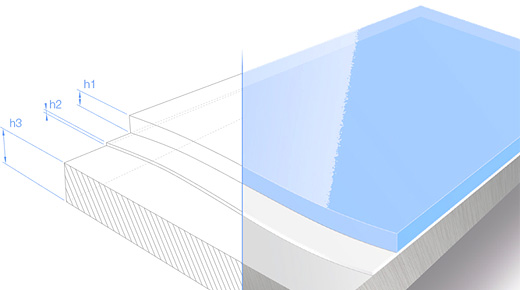
Body
Sponsored Content
Coatings play an essential role in the product development cycle, whether for corrosion resistance, protection against moisture intrusion, or simply to beautify a product. Since over- or under-application can lead to poor performance or product failure, thickness measurement is essential to help production teams deliver quality products while also controlling costs.
ADVERTISEMENT |
…
Want to continue?
Log in or create a FREE account.
By logging in you agree to receive communication from Quality Digest.
Privacy Policy.
Add new comment