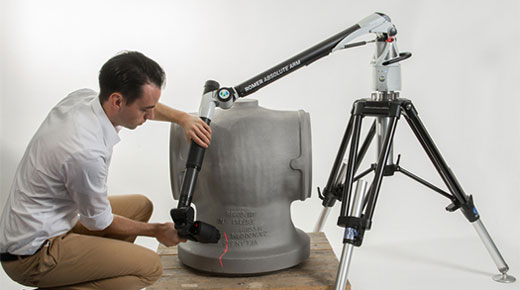
Sponsored Content
Every day, quality and production process leaders must find new ways to improve product processes in a constantly changing manufacturing environment. For most companies, the low-hanging fruit of process improvement is a distant memory. Now, it’s all about seeking significant improvements in the smallest production details to lower process costs and raise efficiency and accuracy.
ADVERTISEMENT |
In the advanced manufacturing world, every minute saved in product measurement and dimensional verification extrapolates to significant daily cost savings. From a measurement standpoint, increased measurement accuracy enables incremental and major process improvements. Thus, today’s process improvements must come faster and be more accurate today, a defining aspect of modern metrology solutions like 3D laser scanners.
…
Add new comment