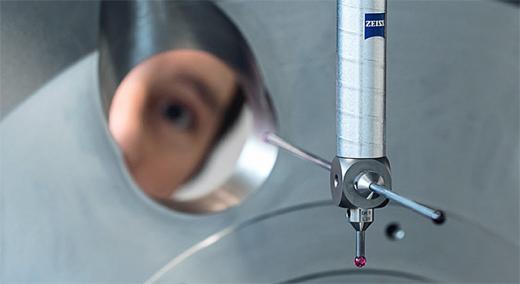
Decanter centrifuges from Hiller GmbH, headquartered in Vilsbiburg, Germany, are in demand globally. These centrifuges separate solid and fluid materials, such as in the production of olive oil or wine, or for wastewater treatment. The multiton machines achieve high yields unmatched by competitors, thanks to Hiller’s unwavering commitment to precision. Recently, the company acquired a ZEISS ACCURA to help it deliver on this promise.
ADVERTISEMENT |
Dietmar Heller, Hiller’s plant manager, holds up a small bottle to the light and gently shakes the liquid inside back and forth. It has a golden yellow color with just a hint of green. Any gourmand would identify the substance immediately: olive oil, the best kind, even. A brief taste confirms this: the premium oil has a pronounced olive flavor, but there is no stinging aftertaste. “Extra virgin, extra natural” is written on the bottle, and Heller would swear this is true. He knows the producer of this outstanding olive oil from the south of Spain personally. Moreover, Heller knows a lot about the decanter centrifuge, in which the oil is separated from the solids and water found in the olive paste following the harvest.
…
Add new comment