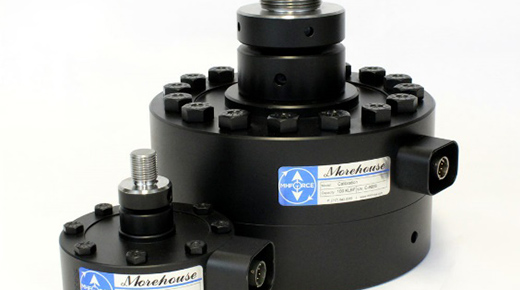
Load cells are a combination of metal, strain gauges, glue, and more. Over time, fatigue ensures that there will be some instability in the system. Load cell stability or drift is usually assumed to be the amount of change in the entire cell system from one calibration cycle to the next. It is the relative standard uncertainty of a reference force transducer’s long-term instability. In an uncertainty budget, load cell drift can be referred to as either the reference standard instability or the reference standard stability.
ADVERTISEMENT |
Load cell stability can impact the following:
• Potentially consume your uncertainty budget
• Cause the force measuring device to be out of tolerance
• Cause all measurements between the last calibration and the current calibration to be recalled
• Raise the accuracy specification of the system
…
Add new comment