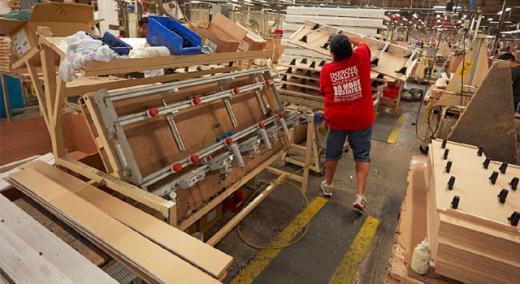
On factory floors all over the world, 3D printing has quietly moved from a prototyping novelty to an essential tool. Advances in printer technology and material science mean that today’s 3D printed parts are robust enough to hold up to real-world wear and tear, and precise enough for demanding production requirements. Today, when production engineers look to maintain quality, reduce cost, or boost efficiency, they are turning to 3D printing to get the job done on time and on budget.
ADVERTISEMENT |
Shortly after Ashley Furniture, the world’s largest furniture manufacturer, brought in the company’s first Formlabs stereolithography (SLA) 3D printer, one of their production engineers decided to try replacing machined alignment pins with 3D printed parts. If these held up to constant cycles and impact, the company could avoid the long lead times and minimum-order quantities of outsourcing the production of the alignment pins.
…
Add new comment