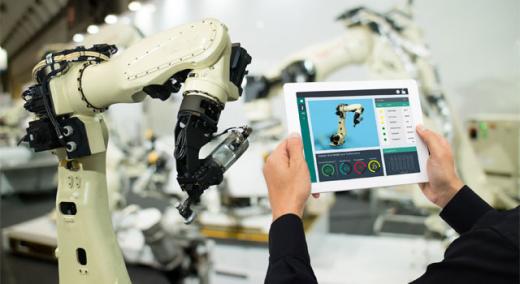
We are all familiar with flash memory storage devices, the inexpensive “thumb” drives that you stick into your laptop to store and transfer data. However, there are much more rugged industrial flash drives that perform mission-critical storage functions built into systems that you rely on almost every day. You can find these in healthcare imaging, diagnostic, and therapeutic equipment; in aerospace for jet mission data collection, unmanned aircraft base stations, in-flight wi-fi services, and flight recorders; and in transportation for controlling a locomotive subsystem, recording event data, and launching the operating system for a commercial vehicle tracking system.
…
Add new comment