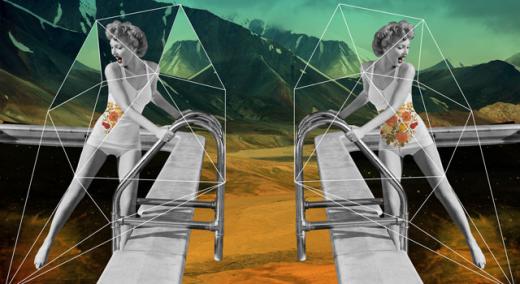
"Twins" Credit: Aaure
Today thousands of technologies and solutions help businesses improve efficiency, create better products, evolve faster, and so on. A digital twin is a technology that deserves a closer look, especially if your goal is to improve business performance and reduce costs.
ADVERTISEMENT |
What’s a digital twin, and how does it work?
In the simplest terms, a digital twin (DT) is an exact, detailed, and dynamically updated digital replica of something in the physical world (e.g., objects or processes). A digital twin is run in a simulation environment to:
• Monitor performance and efficacy
• Test different scenarios
• Predict issues
• Find optimization opportunities
Unlike traditional computer-aided design and engineering (CAD/CAE) models, a DT receives live data from its real-world counterpart and changes accordingly through its life cycle.
…
Add new comment