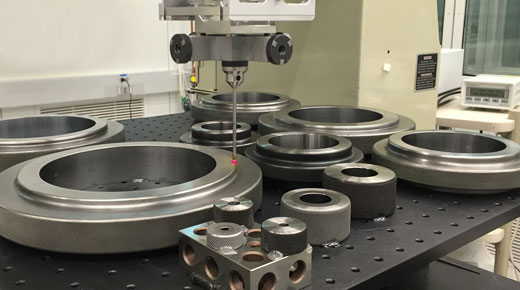
The National Institute of Standards and Technology (NIST) is home to one of the most sensitive machines in the world for measuring objects’ dimensions. Customers who rely on the instrument include the military, academia, instrument manufacturers, private industry calibration labs, and more.
ADVERTISEMENT |
Recently, NIST staff added a second machine with comparable sensitivities. Thanks in part to the new addition—nicknamed “Bob”—NIST is now able to take on more specialty measurements for industry. Staff are currently working on a request from a manufacturer to measure the dimensions of high-precision custom parts, a departure from the usual high-precision standardized objects they measure.
A set of ring-shaped gauges sitting on one of NIST’s coordinate measuring machines (CMMs). The ruby-tipped shaft (center) is the touch probe.
…
Add new comment